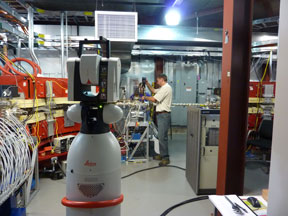
The “CT” in CT metrology stands for “computed tomography” and is a form of “non-destructive testing.” A certain form of CT metrology has been used for inspection purposes for decades in the 2D space. It involves capturing an image of an object in order to evaluate that object for cracks or pores that might have formed during the manufacturing process. At Exact Metrology, we take that work a step further and use CT metrology in the 3D space for greatly advanced inspection and analysis of manufactured objects.
CT Metrology Explained
3D CT metrology involves capturing images of objects in three dimensions to create a voxel (short for “volumetric pixel”) dataset. These datasets are highly valuable for reverse engineering as well as inspection purposes, including those involving traditional structured light and laser-based data capture.
The major advantage of 3D CT metrology, as opposed to traditional 2D methods, is its ability to capture internal data in a non-destructive manner. Traditional methods require that an object be cut into or dissected to truly inspect its interior. With 3D options, you are using advanced X-ray technology that provides comprehensive information about an item’s volume, mass, and interiority, including porosity and density.
Evaluation of Porosity
One aspect of inspection that a CT metrology approach is particularly valuable for is an analysis of porosity. Porosity can be a serious issue in metal and plastic manufacturing as small and large voids alike can be detrimental, even catastrophic, to the integrity and functionality of a manufactured item. While traditional 2D X-ray processes can identify the existence of these voids, advanced 3D processes facilitate the evaluation of their exact size and positioning. This evaluation in turn allows for the plotting of void and crack trends, which can lead to positive adjustments to the manufacturing process moving forward.
Evaluation of Density
In addition to in-depth inspection of porosity, CT metrology also allows for a closer look at the density of an object. Evaluation of density provides insights into how various components are interacting with each other and fit together. This is also the stage at which you can assess if components have been fused together properly, such as with ultrasonic welding processes.
Through 3D scanning, materials can be digitally separated and evaluated independently of one another, based on their density. In addition to serving inspection purposes, this digital separation can also be used for reverse engineering, using the digital data to create a model object as well as construct details of its assembly for future use.
Contact Exact Metrology For More Info On CT Metrology
Now that you know some of the basics in terms of the definition of CT metrology and how it is used, you may have some ideas about how these processes could benefit your own industry or organization. For inspection purposes, reverse engineering, or otherwise, Exact Metrology offers a couple of different options: You can either purchase metrology equipment to conduct these processes in-house or you can turn to our 3D scanning services and rely on our expert team to do the work.
To learn more about these options, use our quote request option to reach out! We look forward to hearing from you.