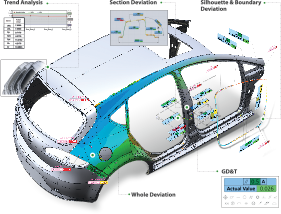
Precision is crucial in manufacturing settings. Because there are multiple ways to achieve the accuracy necessary to design and manufacture high-quality parts and products, it’s useful to know the differences between industrial measuring systems. There are several differences between CMM and 3D scanners for manufacturing that are beneficial to understand. Moreover, knowing more about measurement technologies will give you insight into ways to enhance your team's workflow, reduce inspection time, and give you greater capability when tighter tolerances are demanded.
Key Differences Between CMM & 3D Scanners
A few key differences distinguish CMMs and 3D scanning technologies. If you’re familiar with traditional CMM technology, you may be wondering how 3D scanners work and why are they worth investing in. There are differences in how each tool measures, the age of the technology, the quality of their components, and their portability, to name just a few. First, we’ll delve briefly into the differences between CMMs and types of 3D scanners.
CMM
A CMM, which is short for Coordinate Measuring Machine, is a machine that measures the dimensions of an object by mapping a series of geometric points with a probe. CMMs have been around for a long time, and have been used in countless manufacturing and industrial applications. A CMM is a metrology tool that uses contact measurement, meaning that it must come into physical contact with whatever is being measured to ensure accuracy and to create the data points to develop a prototype or digital model. Traditional CMMs are stationary, which means that they must be used in the setting where they are installed, though PCMMs (Portable Coordinate Measuring Machines) are an excellent option if you need portability.
3D Scanner
A 3D Scanner is a machine that can measure the exact dimensions, textures, and imperfections of any object. 3D laser scanners can capture digital scans of the external geometry of an object. 3D scanners achieve this through laser and white light scanning. Laser scanners and white light scanners are two common types of 3D scanners for sale on the market today, which can easily create digital models of scanned objects through paired software. The various measurement ranges of 3D scanners give you the ability to scan an object as small as a grain of salt to as large as a football field. There is a 3D scanner that will meet the needs of your application.
Advantages of 3D Scanners for Manufacturing
There are multiple benefits to using 3D scanners in a manufacturing setting. Whether you are capturing 3D digital data for the aerospace, automotive, medical, or plastics industries, there is a 3D scanner that aligns with your speed, accuracy, and cost requirements.
Highly Portable
The portability of a 3D scanner is what makes it so adaptable in industrial settings. With the ability to use a portable 3D scanner as a shop floor solution or in multiple locations to collect large data sets, you are able to scan effectively and more importantly, safely. Exact Metrology implements 3D measurement systems from the metrology industry's leading manufacturers, making sure you are equipped with the right tools for all your inspection and reverse engineering needs.
Extreme Accuracy
One of the most important elements of 3D scanners is their extreme accuracy. We know that no matter what industry you’re manufacturing in, your part needs to meet tight tolerances and complexities. Whether you’re designing a part that will be installed in millions of automobiles or you’re creating a one–of–a–kind prosthetic in the medical field, accuracy to the nearest micron matters. 3D scanners are capable of collecting a much higher number of data points, over 1 million points per second, resulting in a 3D model with an unparalleled level of detail.
Increased Speed and Flexibility
Reduced inspection time and increased productivity is needed in any industry. If you are performing a design verification process, such as a First Article Inspection, having 3D scanning technology at your fingertips can give you confidence that small deviations and variations can be found before many parts are manufactured.
In addition to prototyping, 3D scanners give you the flexibility to reverse engineer in software, allowing you to extract as-built information from a part in order to duplicate or enhance the part. However, reverse engineering applications in manufacturing settings extend far beyond product design. In addition to design, 3D scanners can be used to archive a single part or an entire facility. These scans can be used to create a complementary part or to give you the power to plan a more efficient design for the equipment in your space.
3D Scanners From Exact Metrology
Exact Metrology uses, supplies, and services 3D scanning solutions from the metrology industry's top manufacturers, with a versatility of use in a wide array of industries. Understanding the requirements of manufacturing and other heavy industries, we can point you to the right 3D scanning system and accompanying software that is the right fit for your application. Contact us today to learn more about the 3D scanning services from Exact Metrology.