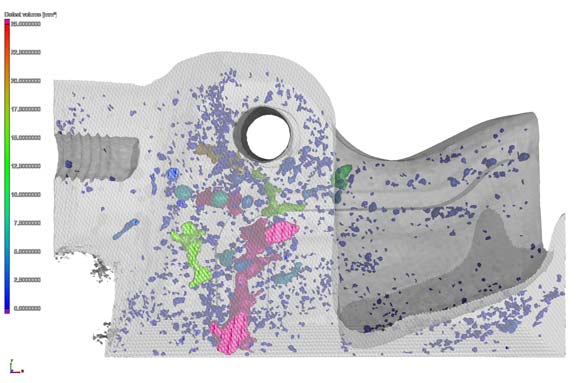
In this blog, we explore a few of the numerous advantages of using industrial CT scanning for your inspection process, to improve inspection throughput. Incorporating CT scanning can make your inspection process more thorough and more reliable, ensuring that you have accounted for more micro details and components of manufactured items. Read on to learn about three of the main ways that CT scanning can benefit industrial inspection: Through x-ray technology, efficient and multi-faceted capturing, and high-resolution captures.
X-Ray Core Technology
The first way that CT scanning can benefit your industrial inspection process is through its x-ray core technology, which allows for capturing the internal geometry of an object. This ability can be of utmost importance when inspecting items whose construction involves a complex manufacturing process with multi-component assemblies, such as additive manufacturing, that obstruct internal components or materials. CT scanning is equally useful for manufactured objects that involve the bolting or fusion of parts.
X-ray capturing of internal geometry during inspection also supports the discovery of inclusions, cracks, and pores, which can be significant discoveries in some forms of industrial manufacturing. For example, processes such as diecasting and injection molding involve limits to the size and number of voids or pores. Being able to identify the position, size, and volume allows for crucial quality control as well as precise modifications of the ongoing manufacturing processes and methods.
Such restrictions and standards are features of the aerospace, automotive, and medical industries. Without the application of x-ray core technology, the inspectors must manually dissect industrial parts in order to evaluate them before applying traditional methods. With CT scanning, no dissection or sectioning is required for fully accurate volume and position calculations and capturing of internal data.
Capturing Multiple Parts in One Go
Another advantage to CT scanning for inspection throughput is that, in many cases, it allows for the capturing of multiple parts in just one setup. While this ability will vary somewhat based on individual part sizing and measurement volumes, the ability to capture more of an item in one setup will be greatly improved in comparison to other inspection methods.
For example, when capturing the components of a drywall anchor using CT scanning technology, over 100 parts can be captured in a single setup. The CT scanning software allows the user to predefine analysis parameters and is then able to distinguish each individual component and then process them in batches. Depending on the defined scan resolution parameters, this efficient process supports the capturing of the scan to analysis throughput in just a few minutes.
High-Resolution Full Surface Capture
Speaking of image resolutions, CT scanning also allows for high-resolution full surface capture, yet another benefit of using this technology for industrial inspection processes. This approach has clear advantages over analog methods for inspection, such as micrometer or digital CMM (coordinate measuring machine), which are both susceptible to error and time consuming.
Instead of piecing together information from hand methods, CT scanning offers 3D data that constructs a complete surface profile. This profile is a topographical map with point spacing down to the micron level. This level of detail allows for the analysis of virtually any geometrical issue that could be present in the object. Additionally, the data supports side-by-side comparison to the 3D CAD model, further ensuring precise and accurate construction.
Turn To Exact Metrology for Industrial CT Scanning
Now that you understand some of the ways industrial CT scanning can improve your inspection throughput, you may want to take the time to explore Exact Metrology’s CT scanning services for a more in-depth understanding of how it might benefit your particular industry. Contact us today with any questions and for more information on industrial CT scanning.